
By Craig Tomita, Area Sales Manager, Universal Robots
For small to mid-sized manufacturers, any gain in productivity can have a huge impact. Automation offers significant advantages, but many small and mid-sized businesses (SMBs) believe that robotics is out of their reach. These organizations can’t afford large, complex robots that don’t fit within their limited floor space, that require specialized personnel to program and maintain them, and that are simply too expensive, with a payback period that is too long to justify the investment.
The new generation of collaborative robots (or simply “cobots”) is changing the game for smaller manufacturers, helping them compete more effectively, offering new opportunities for employees, and even improving worker safety. Look for these 5 essential requirements:
1. Quick set-up
Setting up a conventional industrial robot can take days or even weeks. That’s time and disruption that SMBs simply can’t afford. When you’re ready to automate, you or any untrained operator need to be able to unpack your new robot, mount it, and begin programming simple tasks in a matter of hours. Collaborative robot arms, such as those from Universal Robots (UR), weigh as little as 11 kg (24.3 lbs), and can be set up in less than a day.
Shane Strange, automation and integration specialist with faucet maker RSS Manufacturing and Phylrich in Costa Mesa, CA, had this experience: “Once [the UR robot] actually hit the floor, we got it unboxed and found a stand for it, and within 45 minutes we had it up, powered, and were actually programming the robot, doing simple back-and-forths and pick-and-place.”
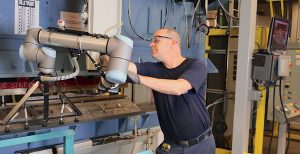
2. Easy to program without special skills
Most SMBs don’t have a robotic programmer on staff—and can’t afford to hire one. But innovative new robotic technology lets operators with no programming experience quickly program robotic movements based on logical process steps and using intuitive tools. When electronics manufacturer Scott Fetzer Electrical Group in Nashville installed a UR robot, line lead Sebrina Thompson found that “If you can program a smart phone, you can operate this robot.”
3. Collaborative and safe, even in small shops
Conventional industrial robots require a large, separate enclosure, which adds cost, takes up operational space, and reduces flexibility on the production floor. Management also has to be concerned with the safety risk if someone manages to get inside the enclosure while the robot is activated. But small manufacturers can’t afford to dedicate large areas to robotic operation. Today’s collaborative robots can work side-by-side with human workers in complementary operations. For example, the innovative force-sensing technology built into UR robots means the robot stops operating if it comes into contact with a human, a vast majority of the thousands of UR robots in operation worldwide work right beside human operators with no safety guarding (after risk assessment).
Robots can take over repetitive, injury-prone jobs and improve worker safety, even in limited manufacturing spaces. Richard Clive, machine operator with shelving manufacturer Etalex in Montreal said, “With the Universal Robot arm now I would say it’s at least a 100% safer. Before you had to put your hands close to the break press… and an accident could happen at any time. With the Universal Robot, there’s no chance of anyone getting injured.”
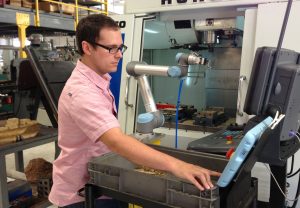
4. Flexible deployment for multiple uses
Dedicated industrial robots can limit small and mid-sized manufacturers who often have small production batches and require fast change-overs. In contrast, new collaborative robots are lightweight, and easy to redeploy to multiple locations without changing the production layout. And with the ability to reuse programs for recurring tasks, they support agile manufacturing processes with minimal set-up time and effort.
Matt Bush, director of operations for electronics manufacturer Scott Fetzer Electrical Group in Nashville was challenged by how to create a mobile robotic workforce when faced with the need for traditional safety enclosures. Mounting collaborative Universal Robots on wheels solved the problem. “When our workers come in in the morning, their task is no longer to do some monotonous task. It’s to go take the robot and deploy it to whatever job it needs to do that day.” With a similar strategy, Joe McGillivray, co-owner of injection molder Dynamic Group in Minneapolis said, “We’re able to quickly redeploy these robots to completely new tasks in very short order. We have most of them—all of them actually—on bases that we can transport around on wheels and slide them from press to press and application to application. That’s been hugely beneficial to us.”
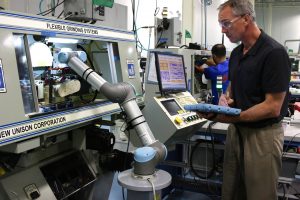
5. Fast payback of your investment
Of course, any automation investment for a small or mid-sized manufacturer must pay for itself as quickly as possible. Collaborative robots give you all the advantages of advanced robotic automation, with none of the traditional added costs associated with robot programming, set up, and dedicated, shielded work cells. And with an average payback period of typically just 2-8 months, robotic automation is finally affordable for small and mid-sized manufacturers.
Hal Blenkhorn, director of manufacturing for medical device manufacturer Tegra Medical said, “We’ve had great financial success with the implementation of these robots, to the tune of what we’re seeing on average for the return on investment of between 3 and 6 months. And we were looking at cost, ease of implementation, and ease of use and the Universal Robots seemed to have nailed it in all those areas.” Dynamic Group’s Joe McGillivray said, “When we first started looking into automation, I was surprised to find that we could afford a six-axis robot, and a collaborative one at that. I assumed those robots cost hundreds of thousands of dollars. The return on investment on our initial system was less than two months.”
Want to learn more? Download the free ebook “How to Get Started with Cobots in 10 Easy Steps”:
Craig Tomita has spent the last 30 years in factory automation, robotics, and machine vision. He was formerly the vice president of IAI AMERICA; and has worked in various
managerial positions including COGNEX, BOSCH-REXROTH, MINARIK, ADEPT TECHNOLOGIES, and most recently, FESTO. Craig is now responsible for managing the distributor sales channels of Universal Robots in the western part of United States and Canada. He is a graduate of the University of Southern California.