Tired of Turnover?
As a manager, do you find it difficult to balance risk and incentives when working toward sales and performance goals? Designing the incentive structures to help your team achieve their best can be challenging. How do you incentivize the correct behaviors and ensure that there aren’t unintended consequences? How do you balance incentives and goals within a diverse team with different interests? Based upon the latest breakthrough research in the field, this program will give you the tools and frameworks to tackle all of those challenges.
Get the strategic guidance you need to exceed your sales and performance goals. In this practical program, you’ll learn frameworks for motivating desired behavior, developing realistic goals, incentivizing teams to rally around goals, troubleshooting and solving relevant problems, and balancing risks and rewards.
Register here
By Brittany Garza
Before moving into my current role, I had no idea what lean was. Lean meant being thin. A green belt and a black belt were visual representations of your skill level in the martial art of Karate. Six Sigma was possibly a fraternity? I knew nothing about the world of lean before jumping in, but I’ve learned a lot these past four years and have loved it. Below are some of the things I wish I’d have known when I started:
- Changing culture is hard and takes time. There are moments when you are going to feel like you haven’t made a difference, and you don’t know what to do next. Find support. Go to conferences. Find a mentor. Inside or outside of your company, finding support will help you get through those down times. The lean community is full of people who are very willing to share and teach what they have learned.
- Customize the tools to fit your company. Not every lean tool will be applicable to your company. Find the tools that fit, and systematically make them part of your company’s culture. As I’ve toured many companies, I’ve learned that no two tools are exactly alike. What works for one company, may not work for another, but the principles are the same. Learn from others, and adapt the tools to fit your needs.
- Don’t try to learn everything all at once. One of the first things I did after starting as the lean specialist, was to try to train everyone in the company on the list of lean tools and principles we had determined we needed in our organization. In the end, it was too much to train on and too much to learn all at once. Learn and train others as you take the incremental steps to improve your understanding.
- The best way to learn is to try. You can watch webinars, read books, attend training, but there is no substitute for experimenting and trying things out yourself. Holding events was scary at first, but now it’s one of the best parts of my job. I love learning about and facilitating improvement on all the processes that make my company operate, and getting to know all the people who help my company be successful. When I use the tools in an event or within my own work processes, I am able to draw from my experiences and increased understanding to use when training others.
- It’s OK to make mistakes. There is a saying one of the lean leaders use, and I use it, especially when I am second-guessing the results of an event: “An improvement is an improvement.” We learn through making mistakes. Every event I hold, every training I give, and every time I deploy a new tool in the company, I learn something new. It’s not about getting it right every time. It’s about trying new things, learning, and improving.
- Don’t give up! It won’t always be easy to get upper management, middle management, and front-line employees on board. John Maxwell says, “The only guarantee for failure is to stop trying.” Lean is a constant journey in continuous improvement. Don’t give up!
Mostly what I’ve learned is that change is hard, it takes time to learn, and you’ll make mistakes along the way, but in the end the results are worth it; not only for your organization, but for yourself.
Useful tools and information:
Lean Enterprise Institute
The Karen Martin Group
Lean Pop-Up SLC
Shmula.com
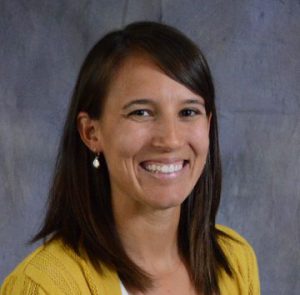
Brittany Garza is a Professional Engineer and Lean Specialist with WesTech Engineering Inc. Her passion for continuous improvement, problem solving, and connecting with others drove her to start the Salt Lake City Lean Pop Up group. Brittany hopes to create a local Lean community that can connect others no matter where they are at on their Lean journey.